FOXTROT International is an oil operator specializing in the exploration and production of natural gas and crude oil that has been operating the CI-27 block in the Ivorian sedimentary basin since 1999.
For several years, FOXTROT International has been the leading producer of natural gas in Côte d'Ivoire with 75% of the supply of natural gas, which contributes 65% to electricity production.
All of FOXTROT International's operational production activities take place on several sites:
- Two (2) FOXTROT (PFA) and MARLIN (PFB) offshore production platforms located approximately 20 kilometers from the coast of the seaside town of Jacqueville and 8 kilometers apart from each other.
- Three (3) onshore delivery terminals located in the municipalities of Port-Bouët (Vridi), Yopougon (Azito) and Jacqueville (Taboth).
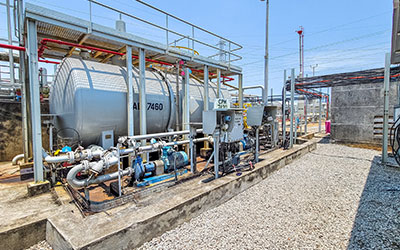
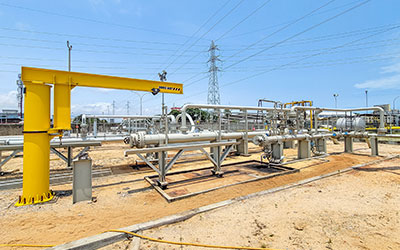
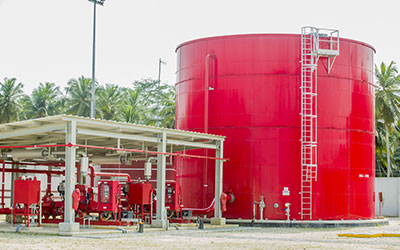
All offshore and onshore sites are interconnected by a network of natural gas transmission pipelines of approximately 300 kilometers and a network of liquid hydrocarbon transmission pipelines (crude oil and condensates) of approximately 130 kilometers.
Description of offshore production sites
Offshore production constitutes all operational production activities that take place in the offshore perimeter, i.e. at sea. These activities are carried out from 2 fixed oil platforms in a water depth of approximately 100 meters, FOXTROT (PFA) and MARLIN (PFB), installed in 1999 and 2015 respectively.
With a maximum production capacity of 154 MMPC/J, the Foxtrot platform (PFA) operates the Foxtrot and Mahi fields and includes 8 wells producing natural gas condensates and crude oil. It includes several units that ensure the treatment of effluents from the producing wells according to the following steps:
Separation, which consists of separating the natural gas, liquid hydrocarbons (crude oil and condensates) and water contained in the effluent at its outlet from the producing wells. It is a series of successive separations until 3 elements are obtained: pure natural gas, liquid hydrocarbons (condensates and crude oil) and produced water. After the separation stage, natural gas and fluids undergo specific treatments to refine their qualities.
For natural gas, we have the following stages:
Compression, which consists of increasing the pressure of the natural gas to facilitate its transport through the pipeline network;
Dehydration, which consists of removing the residual water vapor contained in the natural gas before its export via the delivery terminals, in order to improve its quality and facilitate its transport through the pipeline network.
For liquid hydrocarbons, the condensate and crude oil collected, after the series of successive separations, are dehydrated and stored in a tank and then pumped to the customer through the pipeline network and via the Vridi terminals.
Finally, the water from production at the end of the separation process is treated through decantation and flotation processes before to be discharged into the sea.
As for the Marlin platform (PFB), it has a maximum production capacity of 156 MMPC/D, exploits the MARLIN and MANTA fields and also has 8 production wells. The process for treating effluents from the production wells is generally similar to that of the Foxtrot platform (PFA).
Description of the onshore delivery terminals
All operational activities taking place in the onshore perimeter (i.e. on land) are carried out at 3 main terminals:
- The Vridi Est terminal, commissioned in 1999, which ensures the delivery of natural gas to the thermal power plants of CIPREL, CIE and AGGREKO as well as to third parties (SIR and PETROCI).
- The Azito terminal, also commissioned in 1999, which ensures the delivery of natural gas to the Azito thermal power plant and to PETROCI. This delivery terminal was extended in 2022 with the installation of a new gas turbine phase within Azito OM as part of the new consumers project.
- The Taboth terminal, also installed in 2023 as part of the new consumers project, which ensures the delivery of natural gas to the Atinkou thermal power plant.
The natural gas treatment process at these 3 terminals is identical and is carried out in the following four phases:
- Expansion: This process consists of lowering the pressure of the natural gas coming from the platforms in order to comply with the pressure required by customers;
- Separation: This phase of the process allowsto separate natural gas from liquid hydrocarbons from the expansion phase;
- Metering: This process is used to determine the quantity of natural gas delivered to customers;
- Heating: This phase of the treatment is used to increase the temperature of the natural gas delivered to the customer, in order to protect against retrograde condensation of natural gas in the delivery circuit.
The liquid hydrocarbons from the separation phase are sent to a tank for decantation followed by pumping to the customer.
Description of the gas and liquid hydrocarbon transport network
The transport of natural gas and liquid hydrocarbons from platforms to delivery terminals is mainly done using hydrocarbon transport pipelines. For natural gas, the network consists of 12- and 14-inch gas pipelines and, for liquid hydrocarbons, 4- and 6-inch oil pipelines. Along these pipelines, at regular intervals, valves are installed in valve chambers that allow the flow to be interrupted if necessary.